Custom Four-Manual Rodgers
|
I have upgraded my home concert organ situation with a once-in-a-lifetime opportunity. This is perhaps the most interesting story of my life during the 2020-2021 COVID-19 pandemic. No one in my family got sick, but I came out of this with a four-manual home organ.
Nelson Dodge, who owns my local Rodgers Organ dealership (Church Keyboard Center), sends regular newsletters. I was pleased to hear that he was doing well – both health-wise and financially – during the pandemic. For some reason, I chanced also to visit his Church Keyboard Center company website after his October 2020 newsletter. It was there that I noticed an ad for a used four-manual Rodgers organ. Here is the photo from that ad: |
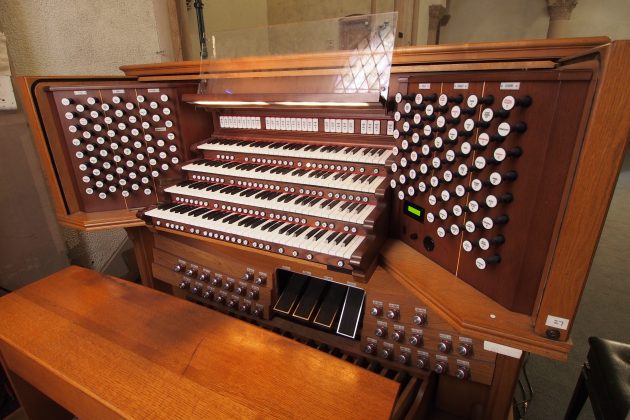 |
I downloaded the specifications from the website and noticed, among other things, that the minimum dimension of the organ was 47". This presented a problem, since the door the organ would have to move through to get to my living room was only 36" wide! I wrote to Nelson and inquired as to the asking price. I then discussed this with my wife, Karen.
Despite the asking price being high, and the fact that we had no way to get the organ into our house, Karen completely surprised me with her response. She said we could replace the front door!
Even though we live in a very large house - especially for Los Angeles – our front door is rather small: |
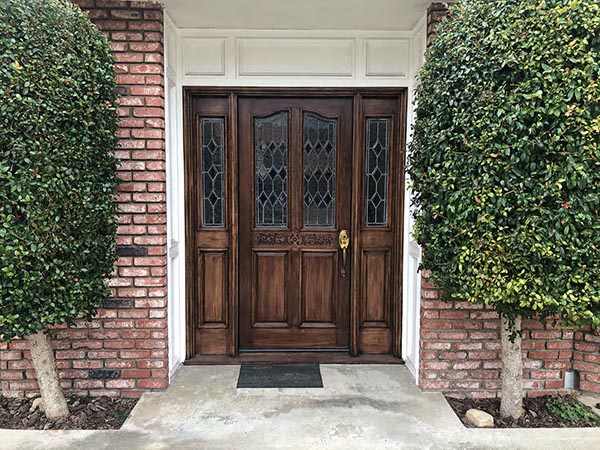 |
I wrote back to Nelson and said we were interested in purchasing the organ. Nelson had closed his showroom for the pandemic and was operating out of his home. Most of the organs were in storage and he was moving them through his garage for clients to try them. We discussed moving the four-manual to his garage so that I could take a close look and do whatever testing I needed to make a decision. I told Nelson that I was in no particular hurry, so this purchase could take a back seat to his regular business.
The time started going by as I found out how busy he actually was. By the time it got to the end of 2020, Nelson wrote to me with a different idea. He proposed moving the organ to my garage rather than his. I could then do my testing at home and no longer be in a long queue waiting for space in his garage. Karen and I agreed to this and the project began to take off.
I should say something about the origin of this organ. Rodgers has, since its inception, built custom organs for customers. Their largest were five-manual instruments and I know of at least three of these. I played one, called the "Royal V" a long time ago when it was installed at my local dealer (two dealers before Nelson!)
This organ was commissioned for the United University Church of Los Angles, California in 1995. Here is a photo of the organ in that church: |
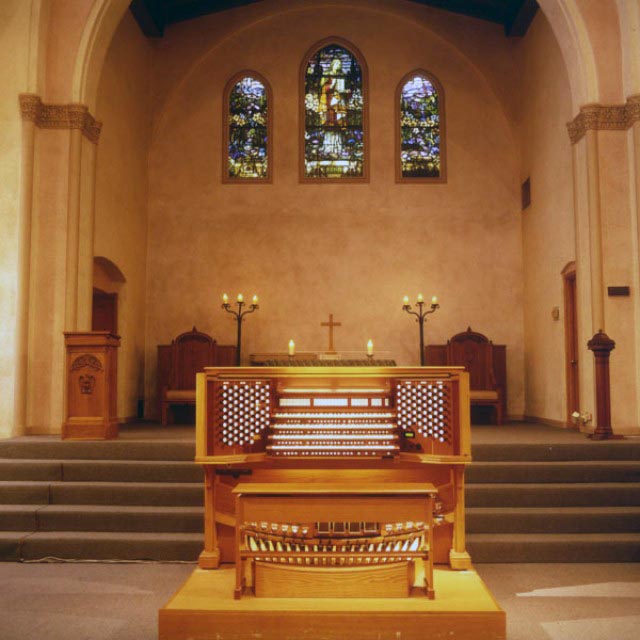 |
This church had a small number of pipe ranks, and the Rodgers organ was designed to control these along with its own digital voices. This is why the organ has two floating divisions in addition to the five divisions one would expect for a four-manual instrument. The "normal" divisions – Great, Choir, Swell, Solo, and Pedal – constitute a very complete American Classic specification. In addition, the pipe ranks formed two divisions: Positiv and Bambarde. This gives the organ a total of 113 stops and 41 couplers – a huge specification indeed.
The organ arrived at our home on January 15, 2021. Nelson contracted with Piano Transport for this. Here is the van arriving at the house: |
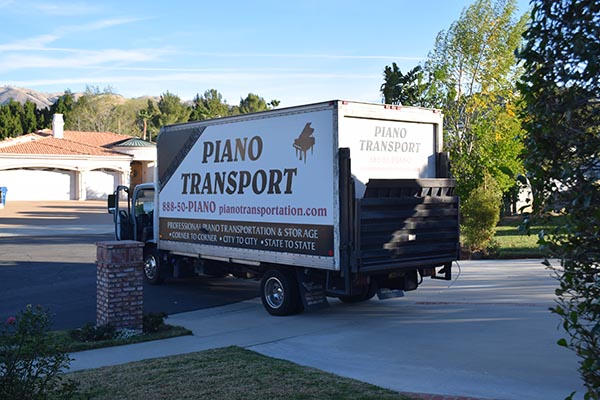 |
I don't mind giving this company some publicity. They did a lot of work! Here is a photo of the three movers wrestling the organ to the ground: |
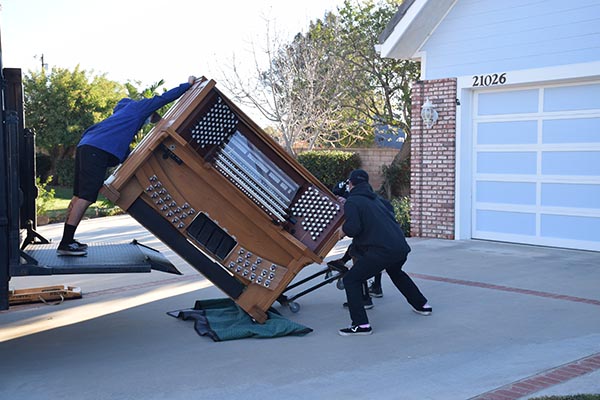 |
This is quite a large console! Never mind our front door, this organ barely fit through a single-car garage door: |
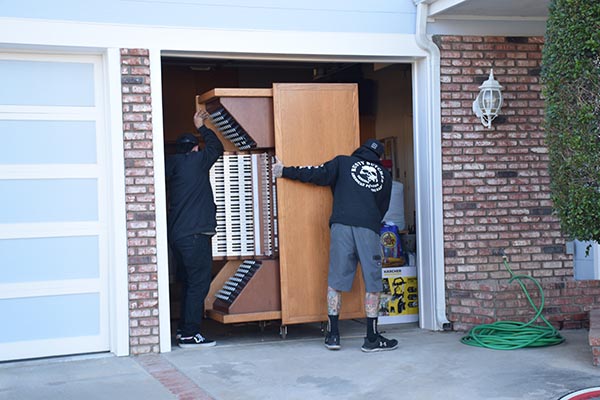 |
With the organ safely in my garage, Nelson paid me a visit that afternoon to get things a bit more set up. This is when I first realized that the organ had no amplifiers.
I had already told Nelson I was not interested in the speaker cabinets that were associated with the organ. I already have seven large Rodgers speaker cabinets in the loft over the organ's eventual location in my living room. I intended to wire the four-manual organ to these speakers, perhaps using a passive mixing network to reduce its 24 channels to seven. However, I had assumed that the console contained a 24-channel amplifier of some sort. After all, my three-manual Rodgers 945 has it's 8-channel amplifier in the console.
This was my mistake! If I ended up purchasing the organ, I would need to buy or build an audio system for it. This was an unexpected, possibly major, expense.
Nelson brought a Yamaha powered monitor system with a pair of small stereo speakers and a bass cabinet. He also brought an eight-channel mixer so that we could listen to a third of the organ at a time!
Here you can see Nelson holding a cable (made by Scott Youngren, Nelson's former organ technician who is now retired and living in Idaho) that connects one of the organ's three sound-generating "cages" with Nelson's mixer. In this way, we can take the output of a third of the organ, mix it to stereo, and listen through the Yamaha speakers. |
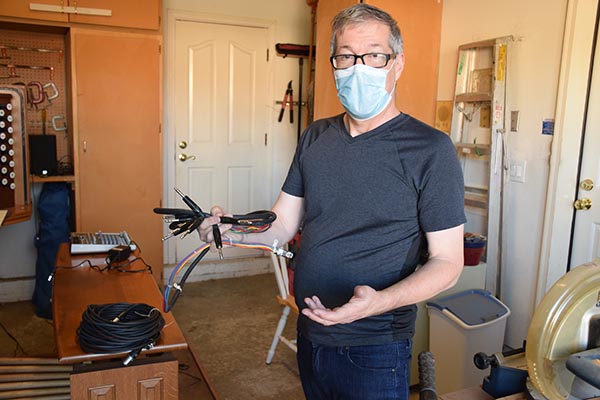 |
While Nelson was here, we tested all three cages. All the organ's internal voices seemed to be working correctly. Here you can see a back view of the console, showing the three cages (on the shelf) and the Roland speakers. |
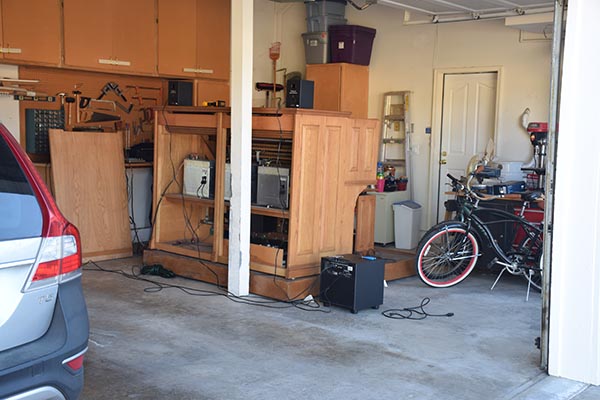 |
After nelson left, I used my laptop to test the MIDI capabilities of the organ. Everything seemed to be working as expected. I dusted the organ a bit and took some publicity-style photos over the next few days. This photo is from January 26.
Notice the platform under the organ. This is from the original installation. I did not intend to buy the platform – but it serves me well in the garage. It allows us to more easily move the organ as needed and provides a natural buffer zone around it to reduce bumps with other things in the garage. |
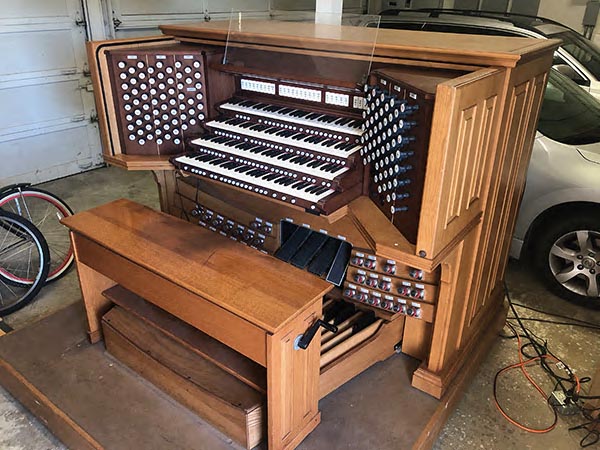 |
I used this photo to create a brochure for the organ similar to what Rodgers would have used in 1995.
I felt very limited in playing the organ with only a third of its voices at a time! I therefore wasted no time in hooking up Hauptwerk (A software-based pipe organ emulation system) to the organ. I moved the Mac Mini and MIDI interface from my Rodgers 945 to the four-manual to accomoadate this. Here you can see the touchscreen monitor sitting atop the console. The Mac is sitting on a box to the left of the pedal board. |
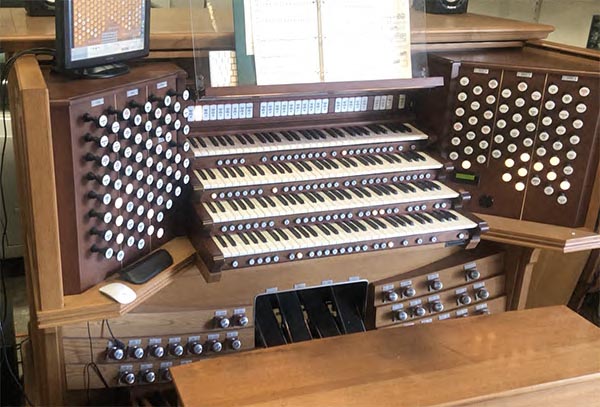 |
This organ is so large, that I only owned a few Hauptwerk sample sets that would do it justice. Two of these came from the First Congregational Church or Los Angeles - the home of the world's fourth-largest pipe organ. I worked on this sampling project, doing all the voicing. This four-manual console does a great job of hosting either the church's chancel Skinner organ or the gallery Schlicker organ. Yes, this DOES mean it would take a console about twice the size of this one to play the entire organ as it exists in the church!
I spent a few weeks playing the organ and noting any defects that needed to be corrected. I also did a lot research into the audio system. When I convinced myself I could build an audio system and the organ met all my requirements, I made an purchase offer to Nelson. The church accepted my offer on February 17 and I released my first video on the instrument to celebrate later that day. Click on the photo below to link to the YouTube video. |
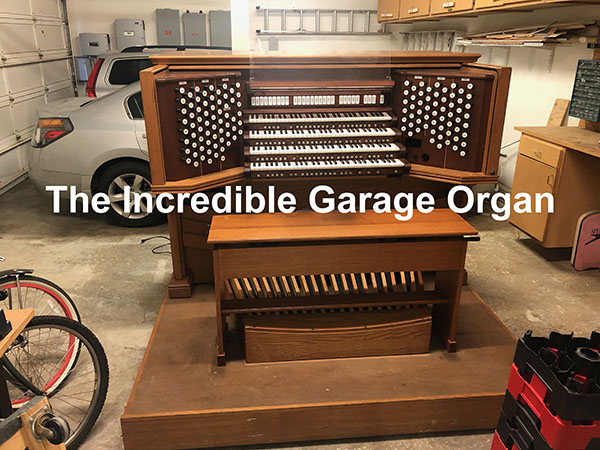 |
I also began working on the audio system on February 17. I had been corresponding with Scott Youngren about this. He recommended that I purchase a Behringer X32 Rack mixer. This is a small form-factor fully programmable 32-channel mixer that can be controlled over WiFi. In this way, I can use an iPad to control it without having to open the console's back each time I need to make a change. Given how massive this organ is, this is a definite advantage. However, the X32 only comes with 16 XLR inputs, so Scott also recommended buying a Behringer S16 Digital Snake. The S16 provides the additional 16 XLR inputs, and eight additional outputs, and connects with the X32.
I ordered the X32, the S16, a small rack that will fit in the lower part of the console, and a rack power unit.
While I waited for these to arrive,I decided I would create a Hauptwerk sample set for this organ that actually matches all the stops and couplers exactly. I wrote to Charles Braund at Silver Octopus Studios in the UK. I have his Concert 85 organ, which consists of 85 stops from ranks sampled in the UK. This has served as my British cathedral organ option on my existing Rodgers 945. However, I need many more stops for the new organ. I proposed to pay the difference in price between his largest set, the Concert 125, and the Concert 85. Charles agreed and I downloaded the 125. Charles also sent me the source file for Hauptwerk's Custom Organ Definition Module (CODM) utility, which saved me a lot of time. I spent a couple days programming a CODM version of the samples that matches my organ exactly including the two floating divisions. The only place I deviated was in the floating Positiv division. Instead of recreating this, I used these stop controls for a floating second solo division which I called "Descant." I placed many solo reeds I had left over in this Division.
Here is a screen shot of the new sample set. |
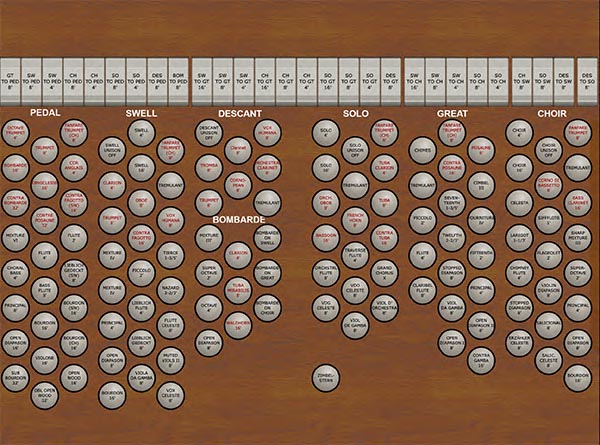 |
The audio hardware I ordered arrived on February 25. I assembled the rack and installed the components. Here you can see the rack sitting in our family room before being moved to the garage. |
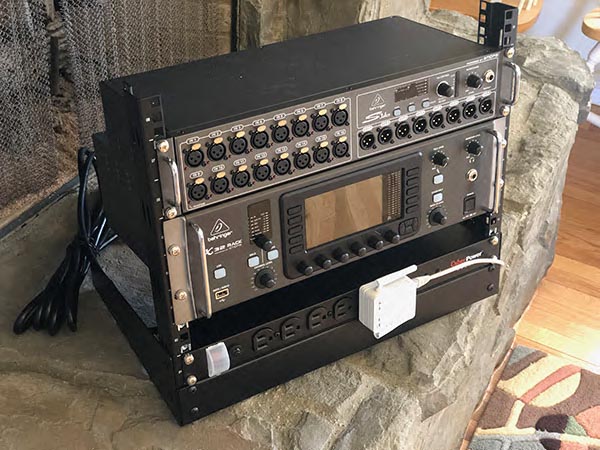 |
The S16 Snake is at the top. Below this is the X32 Mixer. The Power strip is at the bottom. The white object plugged into the front of the power strip is WiFi network extender I had used in the past as part of our home WiFi system. I had not needed it since early in the pandemic when I was able to get the rest of the system working better (by updating firmware.) I reconfigured the extender to connect the X32 to our home WiFi.
Once I verified the system was working, I moved it to the garage and placed it beside the organ on my workbench. |
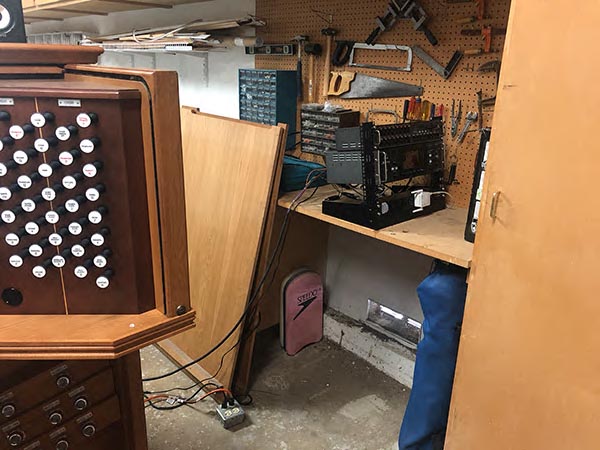 |
I was then able to disconnect the eight-channel mixer that Nelson left for testing. I could use the new rack to play the organ using either Hauptwerk (in stereo) or four channels of the Rodgers internal audio. I was limited to four channels because the X32 only has six unbalanced inputs - two for Hauptwerk and four for the Rodgers.
Since I now owned the organ, Nelson asked Scott to fabricate some parts for the audio system. Scott would build three cables to connect each of the organs "cages" with the rack. The way these old Rodgers digital organs are built, there are a number large computer "cages", each of which generates eight channels of audio. My organ has three of these cages. Scott's cables would have a DIP connector for the cage end and eight XLR connectors for the rack end. Scott would also build a power assembly that connects both to the wall AC and to the switched "organ relay" inside the organ console. Components plugged into the "switched" side oft he organ are turned on an off by the organ's main power switch. Without this mechanism, I would have to control four dirrefent switches each time I wanted ot play the organ!
Nelson will also sell me a Crown rack-mounted eight-channel amplifier that he has in stock. I will use seven of these channels to create the signals to power the seven Rodgers speaker cabinets I already have in the living room organ loft.
Scott's parts all arrived on March 13, 2021: |
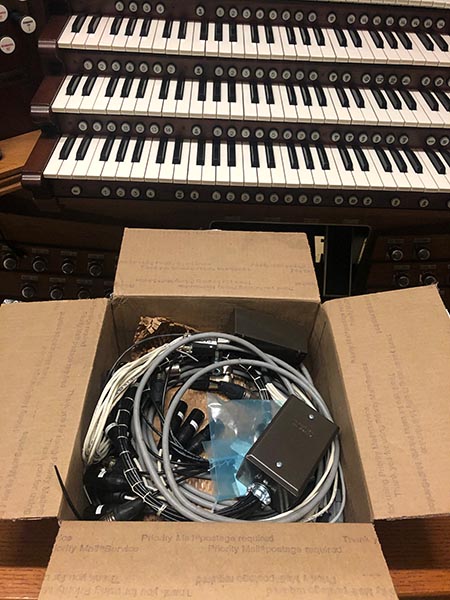 |
The first thing I did was connect the three cables between the organ's cages and the rack. I placed the rack inside the console - not yet firmly attached. I then routed the various cables and programmed the X32 mixer to take the organ's 24 channels and mix them to stereo. I was then able to hear the Rodger's internal voices together for the first time. |
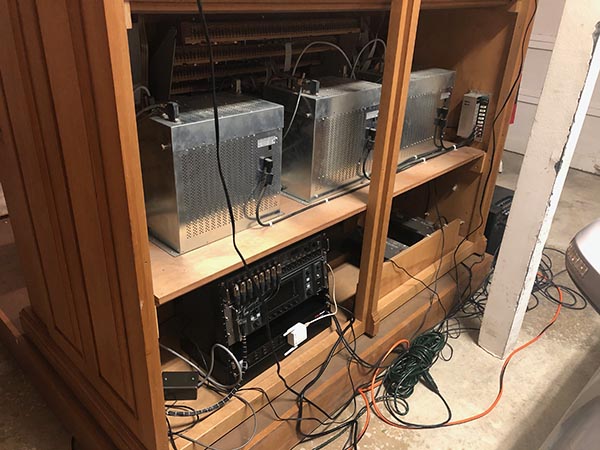 |
I played around with the X32's internal effects processor and programmed some reverb for the organ that sounded very good. My garage organ actually sounded better now than my living room 945 with its external speaker cabinets! I could also click a few buttons on my iPad and switch the organ between its internal sounds and Hauptwerk.
I developed a check list of issues that need to be corrected before the organ is "delivered" into the house. These fell into two categories: those that were related to the console as furniture and those that concerned the electronics of the organ.
I was very pleased to hear from nelson that Bruno Lagarce would be doing the furniture work. I met Bruno on my theater organ project and he is truly a organ furniture craftsman. His main gig is building wooden cases for pipe organs, though he has built or rebuilt many organ consoles. My console will not present much of a challenge for him at all!
Bruno visited on March 26 to fix the few little things on the console. The first was a strange hole that the church had created in the right side jamb. Here is a "before" photo: |
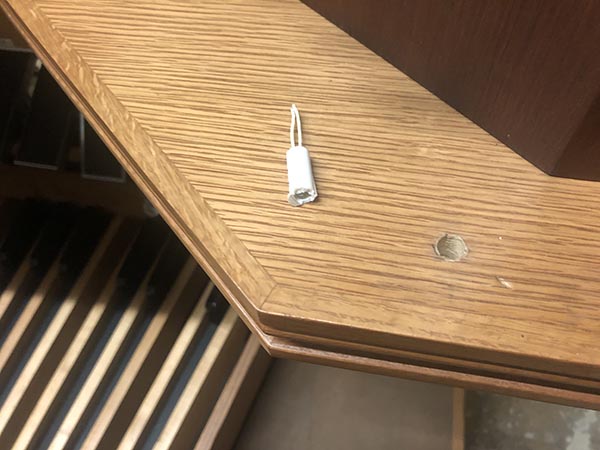
|
The little white plastic plug was in this hole - but I was able to coax it out before Bruno arrived. Bruno brought an oak plug with which to fill this hole. However, he was not satisfied with the fit, so he delayed this fix until he returned a second time.
Bruno was also asked to refinish the top of the organ bench. This job was too big to do in my garage so I helped him carry the bench to his truck. The final thing Bruno did for me (actually, this was not on my list and Bruno did it as a favor) was to cut a hole in the back of the console for the many cables that will have to come out: |
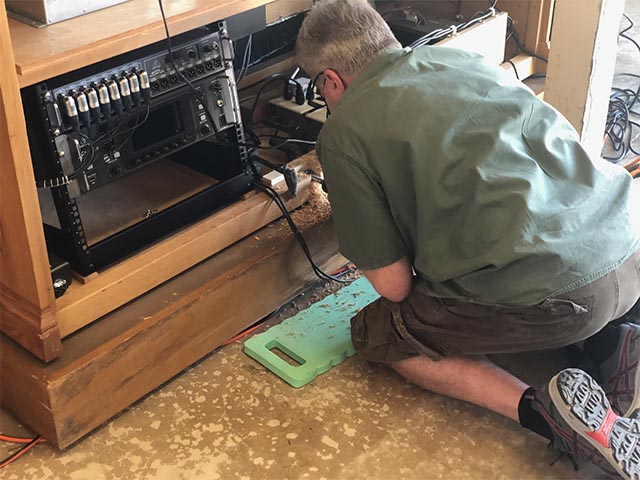 |
I moved the bench from my Theater organ to the garage while Bruno had this bench out for refinishing. In this way I could continue programming and testing the audio system.
Bruno returned on April 2 to finish his work. I helped him move the refinished bench from his truck. It looks perfect now - as if no one had ever sat on it!
|
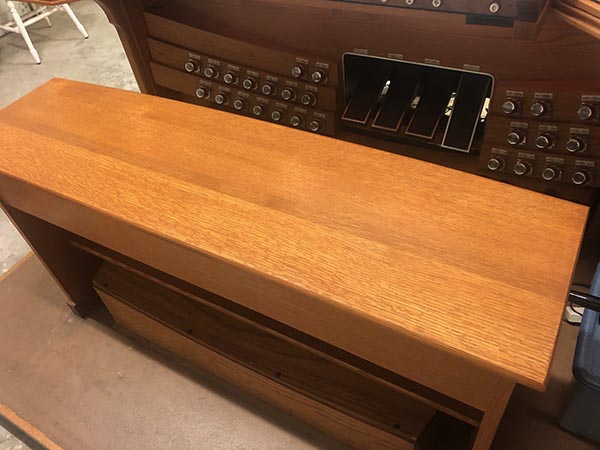 |
Here is the hole Bruno filled in the console jamb. He even managed to match the grain pretty well! It looks even better after it was cleaned up and a matte lacquer was applied. |
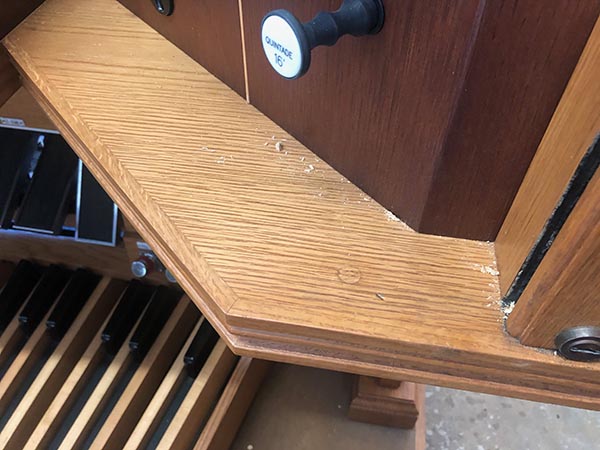 |
Since Bruno's last visit, I had determined that I need even more space for the cables to pass out of the organ, so I asked Bruno to cut a hole in the organ's read panel. We first had to set both panels in place to determine the correct one to modify. Bruno had a great tool for cutting this hole - a sort of electric chisel. |
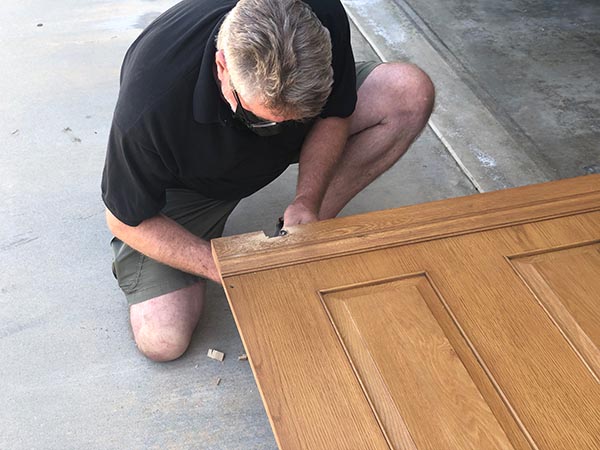 |
Lawrence Strohm (of Strohm Organ Service) was the next person to arrive for work on the organ. Lawrence is a pipe organ technician, but he has taken over Scott's role as Nelson's Rodgers technician too. He came with his wife Biljana. They began ticking repairs off my pick list. Here you see Lawrence disassembling a drawknob jamb to replace some burnt-out stop lamps. |
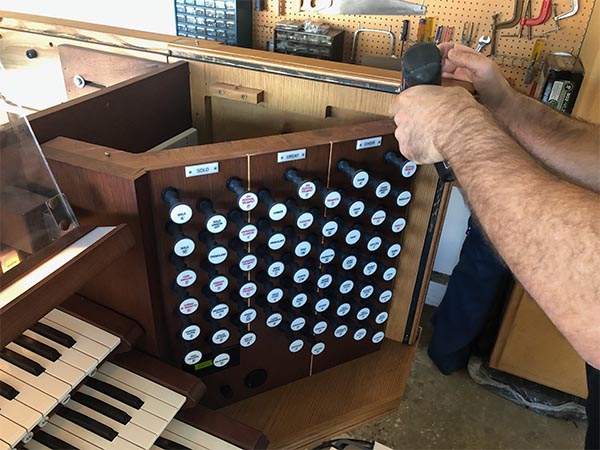 |
While Lawrence worked on the console, Biljana replaced the rubber bumpers (probably a synthetic, actually) on the pedalboard. This will solve problems I have had with sticky pedals and some intermittent contacts. |
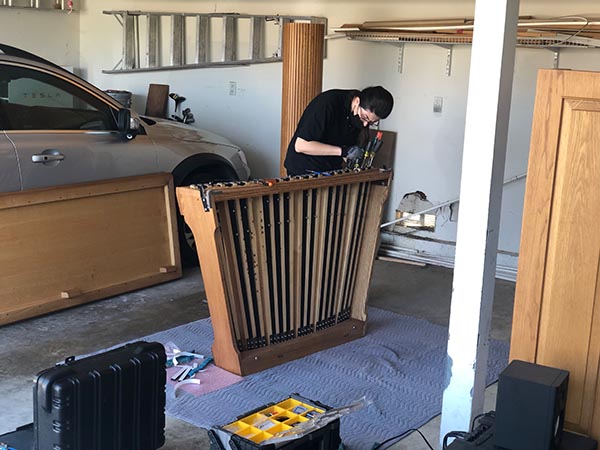 |
Lawrence did a complete cleaning of the key contacts. He removed quite a bit of dust and small debris from between the manuals. He also used a shim to remedy the lowest note on the Solo, which would not return to its "off" position. |
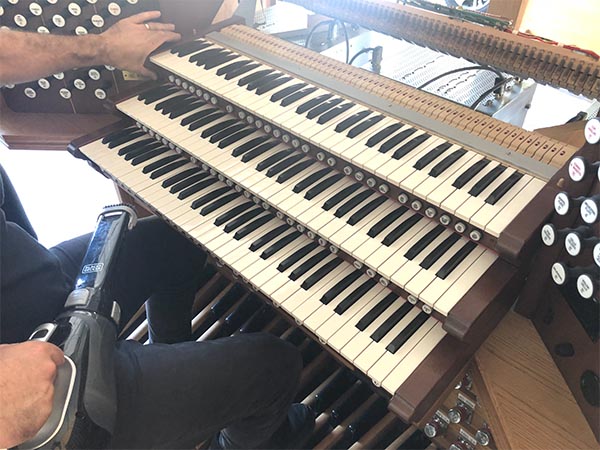 |
Lawrence also delivered the Crown amplifier, but I had no way to use it yet as I do not have speakers for it. Also, Nelson has a small board that attaches to the back of the amplifier to delay it coming on and off while the organ warms up. After the organ servicing, I created another video. This time, I used my new Concert 125 sample set. I also took this opportunity to upgrade my video editing software from iMovie to Final Cut Pro. I was at the end of what I could do with iMovie and my son, Elliot (of Pandemonium Big Band fame), recommended I do this. Elliot even came over to show me some tricks. Click on this photo to watch the YouTube video. |
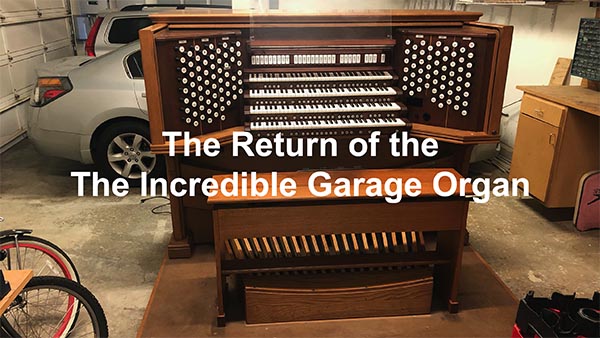 |
I installed the crown 8-channel amplifier in the rack. Notice that the power strip has left the rack! It is not needed because of Scott's power module. I moved the power strip to the recording rack in my studio where it replaces a much older and less capable power supply. This photo also has a good view of the wooden spacers I installed to go between the rack and the organ base. These provide extra wood thickness so I can use longer wood screws to hold the rack in place. These will be needed so the organ can be turned on end when being moved. I have also tied all the cables down using a combination of cable clips and ties. I have left enough slack to be able to turn the rack 90 clockwise to get at the rear connectors for servicing. |
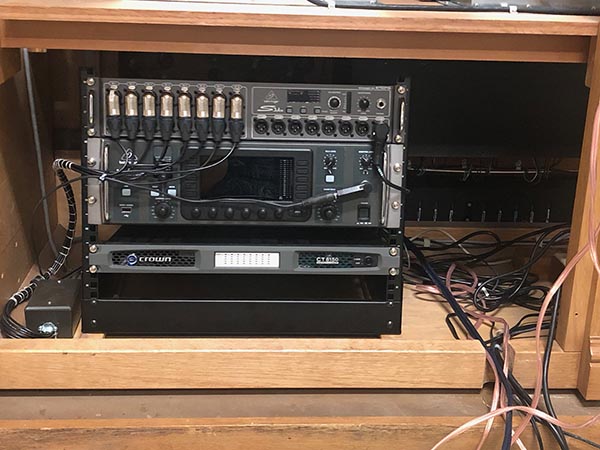 |
I spent a lot of time programming the X32 mixer. I found two old computer speakers and placed them on top the organ - they are the onces closer to the middle of the organ. I attached these to the output of channels one and two of the Crown amplifier. I wired two outputs form the X32 mixer to the Crown channel one and two inputs.
After a lot of programming, I was able to operate the organ in three different audio modes:
1) I could play the all the internal Rodgers voices mixed to stereo through the computer monitor speakers,
2) I could play Hauptwerk samples through the Nelson's powered monitor system, and
3) I could play the organ through headphones using its built-in headphone jack.
The latter requited rewiring the cable inside the console and disabling the contact on the jack that switches off the main audio. |
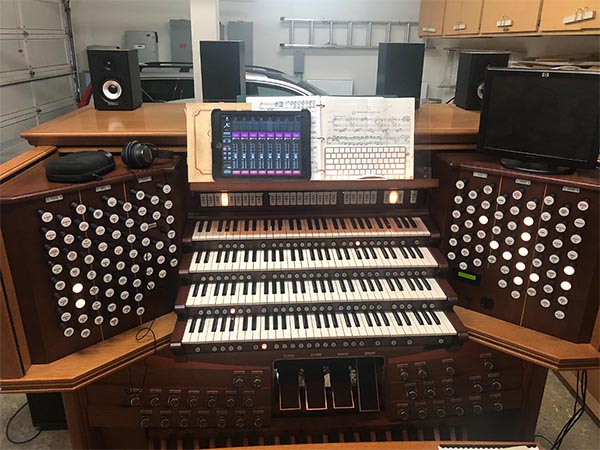 |
Nelson came by on May 15 with the little board that mounts on the back of the Crown amplifier: |
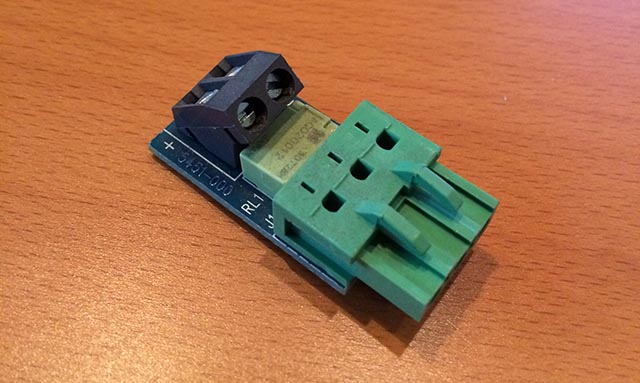 |
It took him a few tries to get the wires from Scott's cable to stay attached to the board! However, it eventually worked. The amplifier now turns on after the organ and turns off when the organ is switched off. Actually, the Crown does not ever turn completely off - it has a sleep state. There is one issue: When the organ is switched off, the Crown makes a loud click that can be heard through the speakers. I need to rememebr to put the organ in "hauptwerk mode" before switching it off.
I created seven cables to go from seven of the Crown's output channels to RCA connectors so I would seldom need to remove the console back again. Here you can see the back panels mounted and all the cables coming out through Bruno's hole. The cables are:
1) The organ's power cable
2) The power cable from the power monitors, which plugs inside the console into Scott's power module
3) Two cables from the mixer for the Hauptwerk sample signal outputs
4) Seven cables from the mixer to the Rodger's speakers
At the moment, only two of the last seven cables are connected - to the two computer monitor speakers atop the organ. |
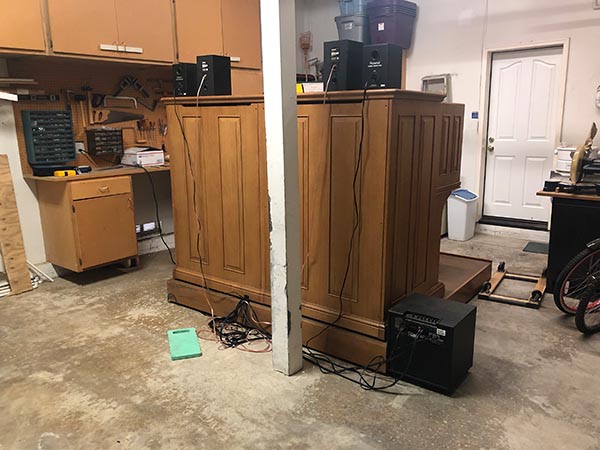 |
I reprogrammed the X32 mixer to the configuration I will use in the living room. Hence, only two channels of the Crown are routed to the little computer speakers now – just the Great left and right channels. This is enough for testing of the Crown's board.
Karen has been working the parallel task to replace our front doors. This has taken quite a bit longer than I had anticipated. The first couple of contractors Karen talked to eventually decided to no-bid this job. I believe the issue is the increase in contractor jobs associated with (what we thoight at the time was) the gradual end to the COVID-19 pandemic in the area. Luckily. I had also asked Bruno if he had someone he could recommend. Bruno suggested James Adkins of Custom Contracting: door/window installations, finish carpentry (818) 886-2339. He eventually took the job.
Meanwhile, Karen had selected doors from Urban Door Company and hardware from Baldwin. The hardware included the ability to lock and unlock to the door from a phone app.
Urban Door said it would take four weeks to manufacture the doors. Indeed, we were notified that the doors had arrived at their store in Northridge on Friday, May 28. Karen and I went to the store to inspect the doors and make the final payment. Karen arranged for someone to deliver the doors to our home on Saturday, May 29. Here you can see Karen looking at one of the doors in our garage - right next to the organ. |
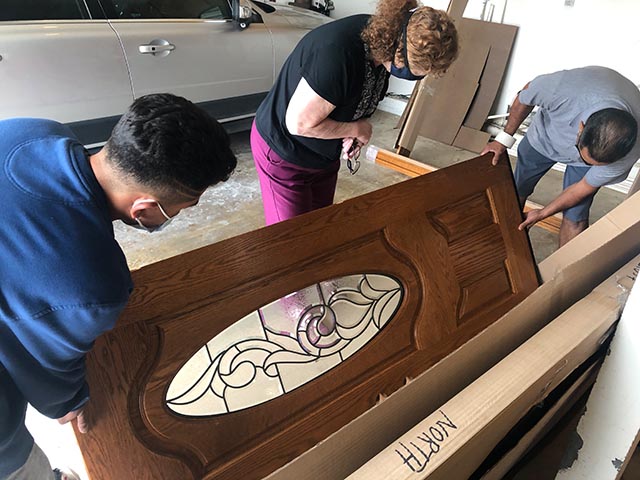 |
James Adkins was able to come to install the doors on Tuesday, June 1. The new doors did not come with a sill, so they open at floor level. This exposed a flaw in our flooring for the first time! There is a small hump in the wood floor that impairs the opening of the left door (as viewed from the inside.) We will have to have our flooring contractor fix this - after the organ move, of course. We will also need a painting and plaster concentrator to tidy up the edges of the new door frame where it meets the walls. All of this will wait until after the organs are moved just in case there is additional damage that will need to be repaired. |
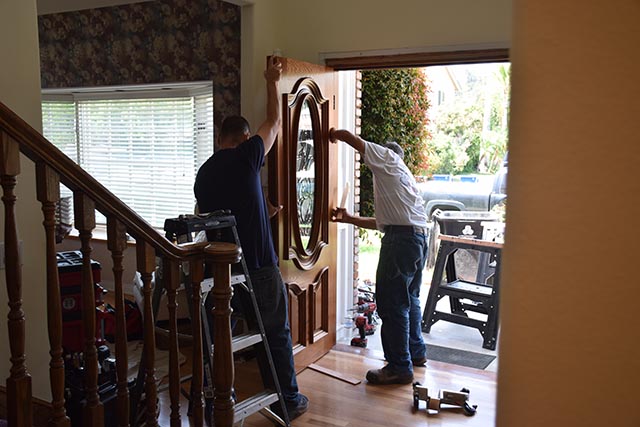 |
This is the front of our house on June1 - it is ready for the four-manual organ to enter now.
|
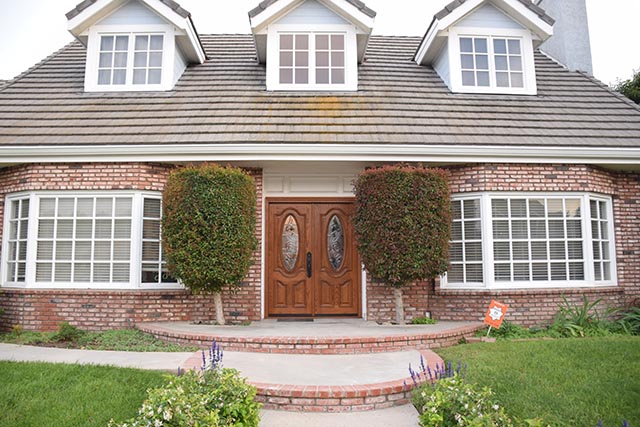 |
It took a while to schedule the Piano Transport people to return for the big organ switch - but the day fianlly arrived on Monday, July 5, 2021. In advanced of this, I prepared both organs for the move. I disconnected everything from the four-manual organ in the garage and moved all the speakers away from the area to make room for the movers. In the living room, I disconnected the 945 from its speakers. I also added RCA connectors to the ends of all the speaker cables coming from the wall so they could plug directly into the connectors coming from the four-manual. Here is the livng the morning of the move: |
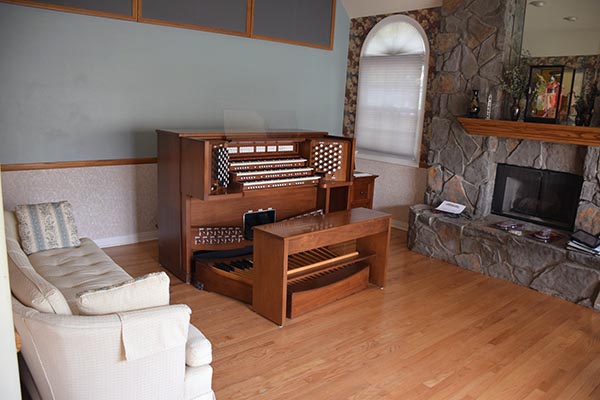 |
They started with the 945 in the living room. This organ - which I used to think of as very large - easily moved through the door and to the garage. Here it is on its way to the garage: |
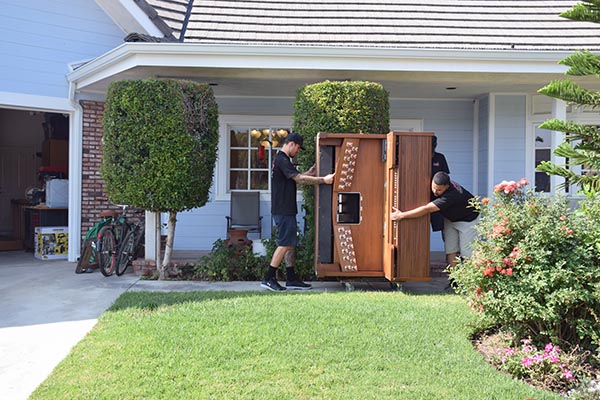 |
Once the 945 was safely in the garage, the movers turned their attention to the four-manual organ. The first step was tilting it off its temporary platform and onto the furntiure dolly. Notice that the rack assembly I bult stayed put as the console was tilted! These guys are strong: |
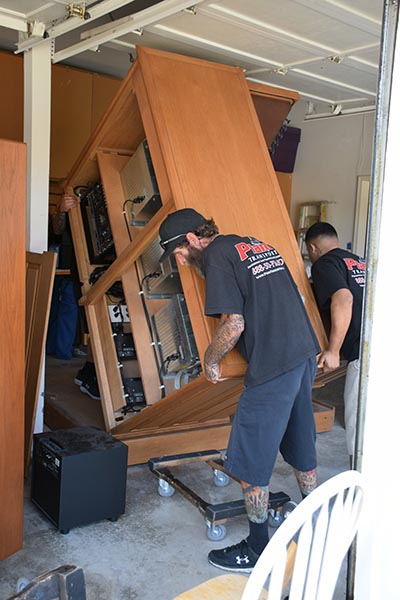 |
And here is the 4-manual making its way to from the garage to the front door: |
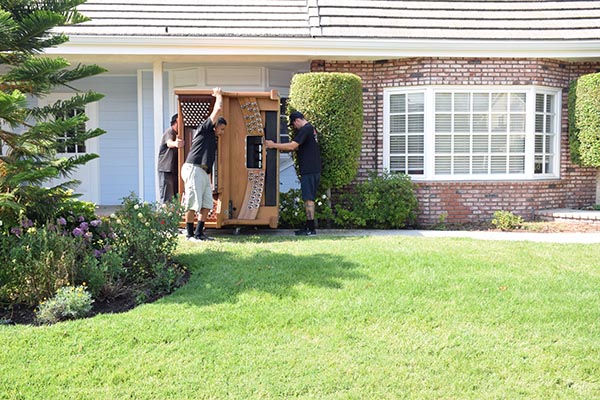 |
Then came the moment of truth - fitting through the new front doors. Of course, this was not a risk because the doors were designed with this in mind! |
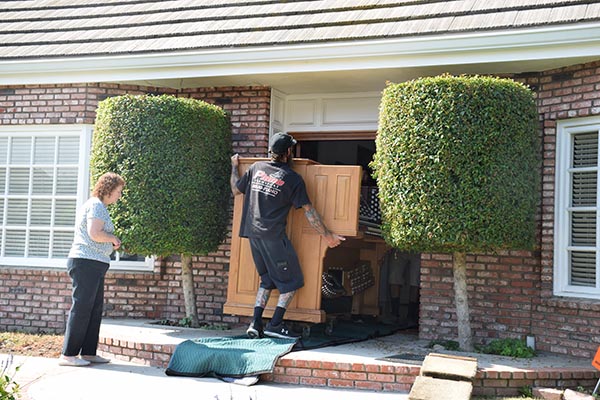 |
The movers left the four-manual organ away from the wall so that I could hook up all the cables. They placed it on some 7" felt sliders I had purchased. I also ordered 2.5" sliders - but the movers told me the larger ones were actually necessary! Karen and I used our regular 1" adhesive felt pads on the pedalboard and bench. Before they left, I verified that I could push the console on my own - which was a great relief to me. It is twice as heavy as the 945 - but it is still possible to slide it on my own. |
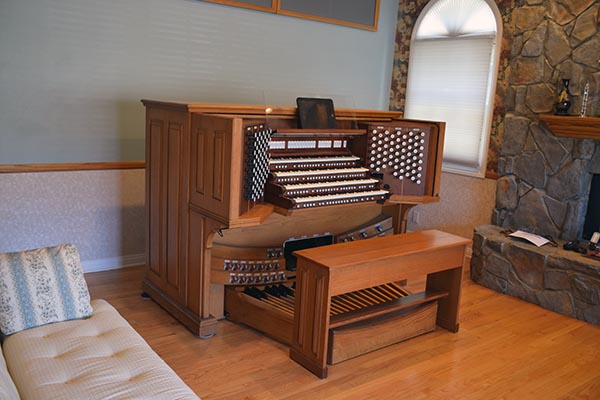 |
There is, of course, a new garage organ - our old Rodgers 945! I hooked it up to play through Nelson's monitor speakers using the organ's headphone jack as the source. Potential buyers can visit our home and try on the organ in the garage. |
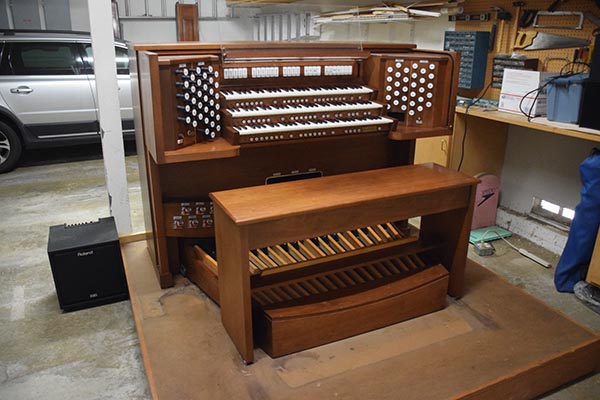 |
After I hooked up all the cables to the four-manual organ, I got it to start only once. After that, it failed to start again. It sounded like it was trying to boot up but failed the boot sequence, shutting down again. After trying this a few times, I called Nelson.
He visited us on Thursday, July 8 and we started trying to diagnose the problem. Nelson quickly discovered that a fuse on the power unit of the main cage had blown. We replaced this with one on of the fuses from another cage and tried again to start the organ, hoping it would at least get further through its boot sequence. Unfortunately, this fuse was itself blown. Nelson took the power supply out of the cage and opened it to see if anything was obviously wrong. When he did this, he discovered a loose screw in the cage! Our theory was that this screw had worked itself into a bad position during the most recent organ move and caused the fuses to blow. Nelson found the right place for the screw and reassembled the cage. Unfortunately, neither of us had spare fuses of this size - so I ordered some online to arrive the next day.
The new fuses arrived on Friday as expected. I replaced the fuses in all three of the organ's cage power supplies. At this point, I was hoping the organ would work - but no such luck! When I tried turning it on, it repeatedly tried to boot and reset a few seconds into the sequence. It was a new behavior - but still not working. I reported this to Nelson and he joined me again on Saturday, July 10.
Based on an experience he and Scott had had on a very similar organ at a Chatsworth Catholic church, Nelson tried reseating the main scanning cable that goes from the main cage's computer board to all of the organ's keyboards and switches. This did not do anything.
Nelson then decided to open one of the two main "black" power supplies on the bottom of the console. It took a while to figure out how to open its chassis - but then it was obvious that a pair of fuses were blown! Once again, neither of us had replacement fuses of this size. However, we were able to place some "almost-correct" fuses in these slots to have a test. The organ turned on and played! We removed the incorrect fuses and I ordered the right ones on line to arrive the next day.
This brought me to Sunday, July 11. I received the new fuses and put them in the black power supplies. I remounted the supplies and turned on the organ - and it did not work! This was a total surprise. Also, there was a new system behavior. The organ tried to boot and generated a pair of error displays repeatedly. It was clearly "almost" working. I sent email to Nelson and Scott, including photos oft hes strange error screens from the organs' digital display.
I then noticed something important. The displays were actually not totally random. The initial boot screen looked like this: |
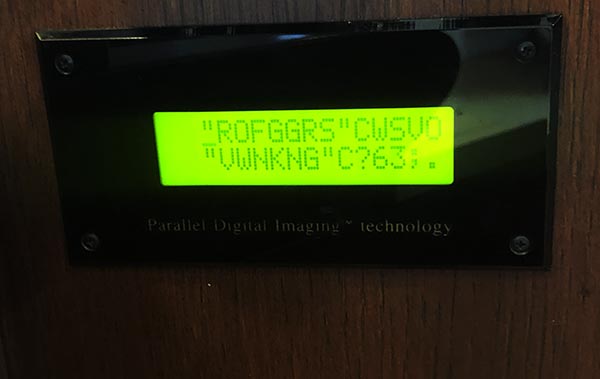 |
Clearly, the organ was trying to display the word "RODGERS"! I checked the ASCII codes for the characters in the display and discovered that the "2's" line was always set to "1". To me, this implied that a wire in a ribbon cable was not seating properly somewhere. Armed with this information, I called Nelson again. He reminded me that he had reattached some cables in the first cage AFTER we did the successful organ test. Clearly this must be the problem. I opened the cage and carefully reattached all the connectors.
I turned the organ on and it played!
However, all if not yet perfect as I now had a loud annoying AC (60 Hz) hum.
The most common reason for AC hum in audio systems is a ground loop. Hence, I ordered some AC adapters that lift the ground (e.g. they are 3-prong to 2-pring adapters). These arrived a day later and did nothing to alleviate the hum - so I knew my problem was not due to a ground loop. I also listened carefully inside the console and determined that the hum was coming from the two black AC power supplies at the bottom right (as viewed from behind).
I did some Internet research and found another effect called "DC bias" that can lead to AC hum. The theory here is that there is a bias in the AC sinusoidal waveshape so that the average value is not 0V. I found a company called Emotive that sells power conditioners that sense this problem and correct it. It took a few days for their conditioner to arrive - but it also did nothing to solve the problem.
Nelson corresponded with the Rodgers factory and suggested that I add some foam under the two AC power supplied. This might cushion the boxes so that their vibrations do not couple as well to the console. This made sense. In fact, I had already noticed that the power supplied used to have a thin layer of foam under their mounting plates, but this had disintegrated with time. I order rolls of 1/4" foam insulation with adhesive backings. These arrived the next day.
I opened the console and removed both power supplies. I added strips of foam to the console as shown here: |
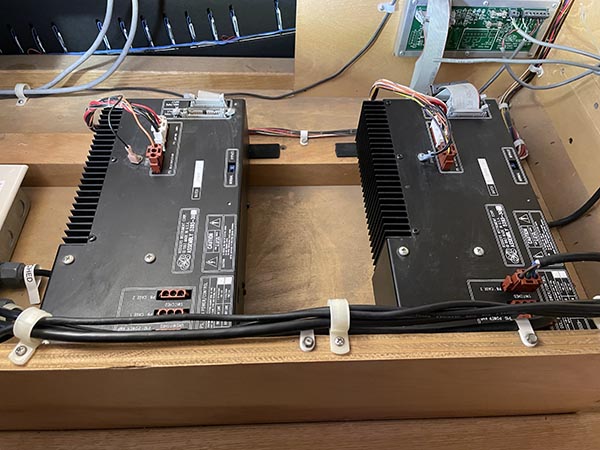 |
Unfortunately, this also did nothing to reduce the AC hum! Nelson suggested that he could replace the large toroidal transformers in these two supplies - but he would need to know the exact part number. I waited a few days and then moved the console away from wall another time. I have become rather proficient in opening the console - which is not something I had planned!
I decided to try another experiment. I removed all cables coming out of the console leaving only the main power cord to the wall. When I turned on the organ it, of course, did not play. However, the hum was essentially gone too! This was another surprise. I connected each cable to see which ones created the annoying hum.
The culprit was the power cord for the Hauptwerk system's powered monitor speakers in the loft. I had connected this to Scott's power box, which in turn gets its switched power from the console's switched power.
I tried one of the ground lifting AC adapters on this cord - but the hum actually got worse!
I then tried plugging the cord directly into the wall. This worked perfectly. I could now play the organ without the hum - or actually with the hum at so low a level that it was not longer bothersome. The disadvantage was that I have to turn the power to these speakers on separately when I turn on the organ.
The following day, I decided to try a cord I had used in the 945 to feed the AC to the loft speakers. I could plug this directly into the console's relay instead of Scott's box. The made no difference. However, I could also plug this into a switched output on the black Rodgers power supply - and this worked fine. This allows the monitor speakers to turn on with the console switch - so everything is fine. The hum must be caused either in the console relay box or Scott's power block. The latter is not likely as I believe there are no active components in Scott's box.
In any case, the project is now complete.
Here is a photo taken on July 23, 2021 using my new iPhone 12 Pro. It is also a test of the phone's camera. If you click on the photo to get the full resolution version, you can read the names on all the stops. |
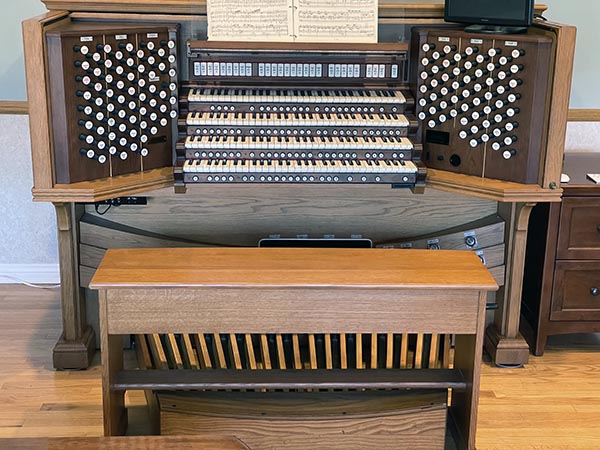 |
|
Postscript:
The Rodgers 945 sat in the garage for a few months but eventually was sold to its new home, a very lucky church! The organ left the garage on March 29, 2022. Our garage returned to its original intended state, a general purpose workspace.
Caltech decided to return to a real in-person full-blown commencement ceremony for June, 2022. I was fortunate that the organ we would rent from Church Keyboard Center is one the brand new Rodgers Infinity systems. Nelson obtained a really nice one for his store - with nearly all the fancy options. It is a three-manual with moving stops, tracker touch, and upgraded cabinet accents. Normally, I would go to the showroom and set combinations in advance of the organ being delivered to Caltech - but since the showroom has not yet reopened from the pandemic, I asked Nelson if it might be stored in his garage. He surprised me by counter-offering to have it placed in my garage between its previous rental and Caltech. Hence, the tradition of garage organs at my house continued!
Here is the Rodgers Infinity Model 367 installed in my garage on June 7, 2022: |
|
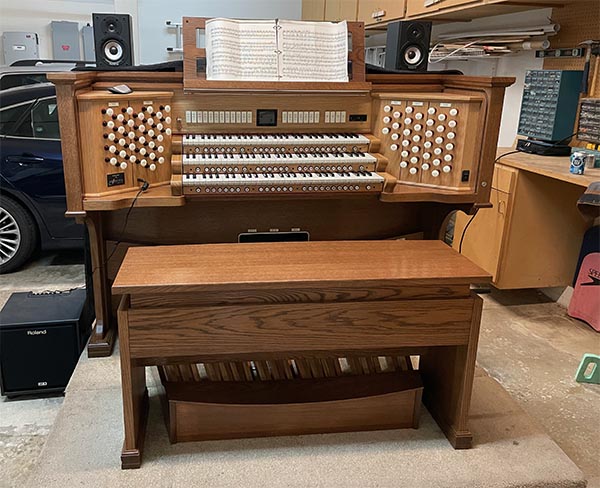 |
|
It stayed here for only two days and then moved to Caltech on the 9th for commencement on June 10. |